Water, gas, electricity – three utilities well-known to any property or business owner. They keep the lights on, faucets running, and stoves burning. If you shift your eyes over to industry and manufacturing, however, you will find that those three do not quite cover all the bases. There is one more utility that businesses in those fields rely on: compressed air.
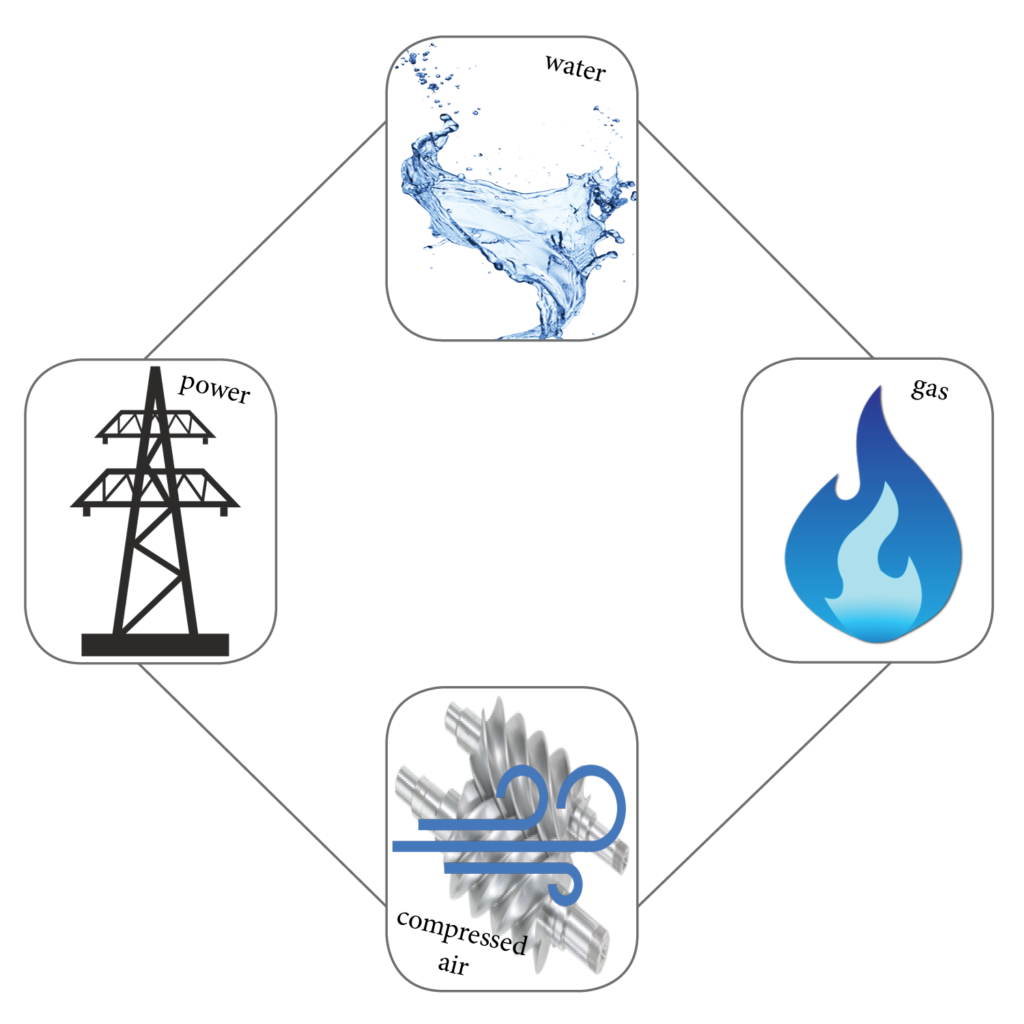
The fourth utility, compressed air, is ubiquitous in almost every sector of manufacturing and industry and is even used by many service businesses: food and beverage, automotive, healthcare, power generation, construction, and agriculture. The applications of compressed air are virtually endless, and countless businesses rely on it each and every day. Few are as familiar with this idea as CompressAir, a leading provider of compressed air services and products in Northern Indiana.
“When I first came to CompressAir, it really opened my eyes to just how many industries use compressed air in their manufacturing process,” Brittany Smith, director of marketing communications at CompressAir, said. “For example, there are large bakeries that use pneumatics powered by compressed air for packaging loafs of bread.”
Just like water, gas, and electricity, running a compressed air system comes with a cost. Just one 50 horsepower air compressor, running fully loaded 24 hours a day at $0.10 kilowatt hours, can cost close to $40,000 in electrical expenses a year.
Unlike the traditional utilities, a compressed air system is located entirely within the customer’s own facility, which means that setup, maintenance, and potential repairs are their responsibility. Left unhandled or poorly attended to, these responsibilities can lead to leaks, oil contamination, heat loss, and other problems that can quickly add up to high, unnecessary costs.
“We see many businesses that have poorly implemented compressed air systems,” Smith said. “There are many factors that must be correct when it comes to ensuring the system works properly. A few key factors are properly sized and maintained compressors, the part load controls must be set correctly, accurate operation temperatures, properly sized and maintained air treatment to prevent moisture downstream, and proper ventilation and correctly sized piping.”
CompressAir is specialized at helping customers install, optimize, and maintain their compressed air systems. In addition to regular maintenance and 24/7 emergency service, its team also provides Air Audits. These are comprehensive reviews of an entire compressed air system that are designed to help your business save money.
“A properly conducted audit supplies a fingerprint of how much compressed air is used as well as when, and if, it is being applied properly,” Smith said. “Once an audit is completed, we utilize a system comparative tool which allows us to simulate operations to ensure energy saving solutions.”
Even traditional utilities, such as energy companies, encourage customers to optimize their compressed air systems.
“In many cases, the solutions an audit provides qualify for energy rebates by utility companies,” Smith said. “Combining energy-saving solutions with rebates make Air Audits very attractive. They help customers run efficiently and can help reduce costs that take away from the customer’s bottom line. An audit can help them be more competitive in their market space.”
CompressAir estimates that an Air Audit can reduce your compressed air system’s energy costs by up to 50% and its maintenance costs by up to 80%.
“We strive to work alongside customers to guide them to a well working and reliable system for their business,” Smith said. “By choosing CompressAir’s team, we can help guide our customers to construct and maintain a system specific to their needs and budget.”
To learn more about CompressAir and how to schedule an Air Audit, visit compressair.net.